Have you ever wondered, “How are vinyl records made?” Well, let me tell you.
Firstly, of course, the music has to be recorded. Sounds obvious, doesn’t it? But without a performance of some description, there can be no record for you to take home and play on your turntable.
After recording, the performance is mixed and mastered for vinyl. “That’s easy for you to say,” I hear you holler. What is mixing and mastering?
Mixing
Well, mixing is the process of making sure that the different strands of music that were recorded are combined to ensure that the overall sound is pleasing to the ear. A good mixing engineer will make sure that they are balanced in terms of their relative volume, but also with regard to their position in the stereo field, be that left, right or centre or anywhere else.
Historical Musical Note:
This stage has been a source of musical sensitivity in the past. For example, Paul McCartney was known to be incandescent with rage with Allen Klein regarding the mix by Phil Spector of The Long and Winding Road along with I Me Mine and Across the Universe on the album Let It Be. At first, McCartney had viscerally berated Klein in his office, only to be met with short shrift by Klein, who claimed to have Lennon’s agreement.
Then there was the major fallout over the mixing of Nirvana’s third and final studio album, In Utero. This resulted in certain tracks being remixed by Scott Litt due to the record label’s unease at original producer Steve Albini’s original mix of the album.
Mastering
Mastering is a more technical post-production stage. It involves the production of a master copy of the album, from which all copies will be made. It involves an element of critical listening. Sound engineers use techniques to optimize playback on a range of different listening systems in a range of users’ homes.
Clearly, with vinyl being an analogue system, mastering is different than for a digital system. For example, dynamic range reduction is usually necessary because vinyl utilizes a physical groove which utilizes quite a narrow range of frequencies. Outside of these frequencies, noise distortion and skipping of the needle could occur.
Creating the master disc
A series of aluminium blanks are sanded so they are completely smooth. Then they are coated in a layer of nitrocellulose lacquer ((C6H9(NO2)O5)n).
This dries to a finish like dried nail polish. Once so, the discs are inspected for flaws. It is absolutely essential that there are none because the final vinyl product will be affected if there are – in essence, your vinyl record may have unwanted sounds or worse, may skip or jump.
At this point, discs which have passed quality control have a hole punched in the centre. They are now ready to be shipped to be cut. Shipping takes place under incredibly stringent conditions. No damage can be caused to the blanks because they will be rendered useless for reasons already discussed.
Although containing no acetate, they are known as acetates.
Cutting the master
At the cutting plant, the discs are removed from their protective packaging and fixed onto the cutting machine, or lathe. They are secured using a vacuum at the centre.
A test cut is made at the outer edge of the master disc before being examined with a microscope in order to check that it is good to go.
Once the mastering engineer is happy, he will begin the process of cutting the master disc. A continuous groove is cut using a sapphire or diamond cutter. Any scrap lacquer, known as ‘hot chip’, is removed with a vacuum suction hose. Careful monitoring of the process ensures that accurate transmission of the recorded sound onto the master disc takes place. Gaseous nitrogen is used to clean the lacquer as it is being cut and methyl ethyl ketone (C4H8O) is used to clean the cutter.
Once the cut is finished, the engineer will yet again do a quality control check to ensure that the disc is perfect. Once he has decided that the disc is of the requisite quality, he will etch a serial number and his initials or even signature in the central run-off or dead-wax area. These will be visible on all pressed copies of the vinyl record.
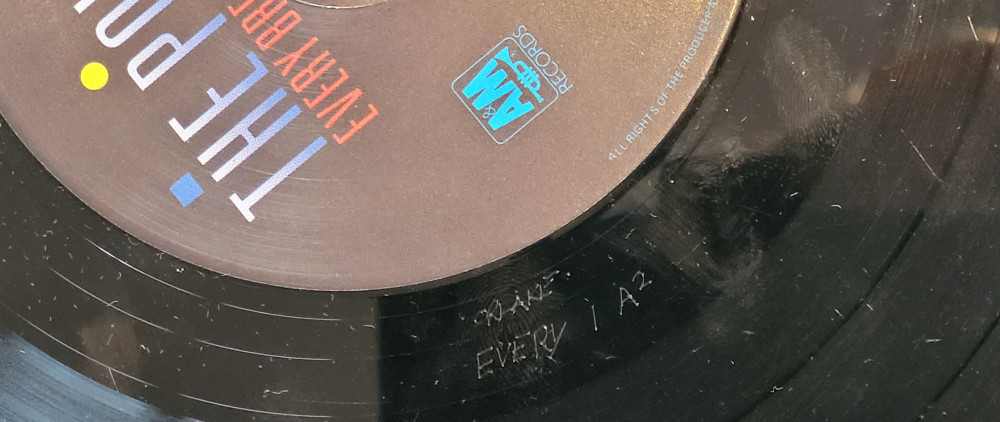
Stamper
Once the master disc has been created, something akin to a negative in photography is made. This is called a stamper and it is used to stamp or press the final products – vinyl records.
But how is the stamper made? First, the master disc must be washed to ensure no foreign objects can contaminate the finished product. Then it is sprayed with silver nitrate. Finally, the disc is immersed in electrically charged liquid nickel.
The positively charged nickel fills the grooves and fuses to the negatively charged silver. Once the process has finished, the nickel disc is removed from the master disc. Where there are grooves on the master disc, we have corresponding mirror-image ridges on the nickel disc – the stamper.
Pressing
Next, we come to the pressing process. The stamper is now loaded into the pressing machine along with a blob of polyvinyl chloride (PVC) and the record label. The press is then operated whereby super-heated steam melts the PVC and forces it around the inside of the press forming a mirror image of the stamper, or a vinyl record.
Once the records have cooled, they are trimmed of excess vinyl and placed in an anti-static sleeve. They are now ready to be shipped for you to buy.
Quality control
Quality control is always paramount during the process, and the pressing phase is no different. Completed records are checked to make sure that they are flat with labels correctly orientated. Samples are assessed using microscopes to ensure that a clean copy of the stamper has been made. Samples are also listened to check for audio quality.
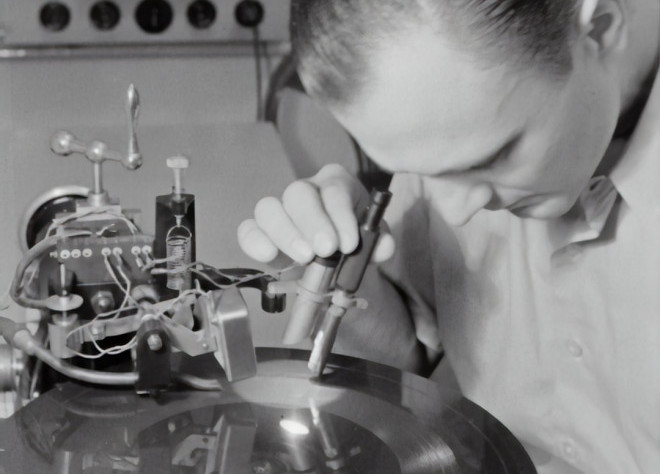
Different coloured vinyl
Different coloured vinyls are used but have different melting points. Therefore, the pressing machines must be set carefully to the correct temperature. Clear vinyl, for example, is much softer and melts at a lower temperature than black. Black is always considered best for sound quality.
Other techniques
Direct metal mastering (DMM) uses a steel disc covered in copper, but no lacquer. At the cutting stage, the groove is cut directly into the copper using a diamond stylus. DMM is nominally the standard method nowadays.
Some people prefer the lacquer method because they feel it gives a more natural-sounding end product. They believe DMM delivers a harsh, metallic sound which lacks the warmth of a cut lacquer version. Others see the benefits of the metal method, especially noise reduction in the final product. This is because with acetates, dust or air particles can be introduced during the spraying of silver onto the lacquer.
However your records are made, it is a great thing that they are still being made and even growing in popularity. All power to vinyl.
If you have enjoyed this article or have anything you would like to add to the debate, please leave me a comment below.